1) User Design - Seat Buckle
ENGR210 Assistive Technology, Stanford University
January 2020 - March 2020
My team worked closely with Danny, a local resident with cerebral palsy and cortical vision impairment, to redesign a wheelchair buckle for users with dexterity accessibility needs. While he has limited sight and control over individual fingers, Danny asked for a buckle restraint that he could secure and remove independently without a caregiver.
We explored several iterations through the design cycle and successfully created a buckle useful for Danny’s everyday activities. The final product features a Neodymium magnetic buckle with wide strap attachments for grip. With a strong magnet, the buckle snaps together without the dexterity and sight required for aligning the typical metal buckles. Our end product can support the weight of ~100lbs leaning against the strap but only requires a slight shear force to slide open.
We utilized design for additive manufacturing for the benefits of lightweight, flexible material with varying strength across ergonomic shapes. 3D-printing was particularly ideal for mid-print magnetic inserts. Low resolution and exposed in-fill geometries increased the grip of the strap. Print times for a small-sized product made for efficient prototype turnarounds.
My team iterated through material, structural integrity, and aesthetic to build a final product that could be immediately used by our user. While we created the product primarily for Danny as an individual, the concept of accessible magnetic buckles are applicable across the assistive technology industry and more.
2) Simulation and Algorithmic Modeling
ME127, Stanford University
April 2020 - June 2020
I have worked with both shape optimization and generative design as methods for additive manufacturing. Below you can find a slideshow of various projects completed within these topics.
# additive manufacturing, needfinding, shape optimization, generative design, FEA, materials
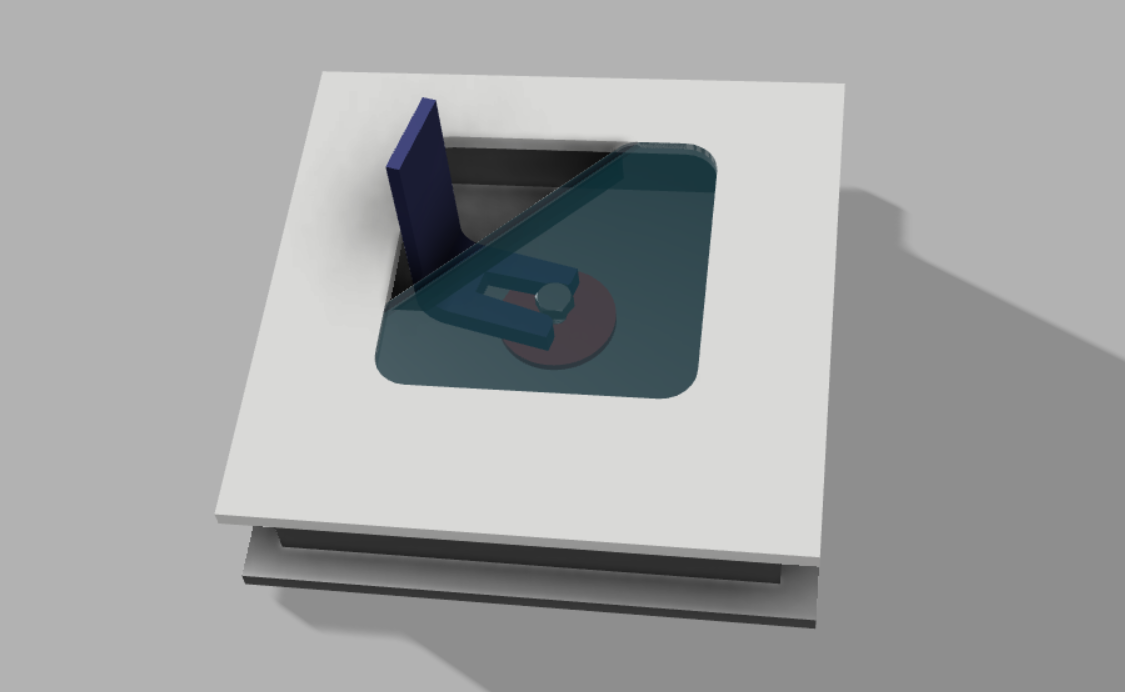
"Space Wrench" - Practice with tolerances and material selection

"Space Wrench" - Practice with tolerances and material selection

"Space Wrench" - Practice with tolerances and material selection
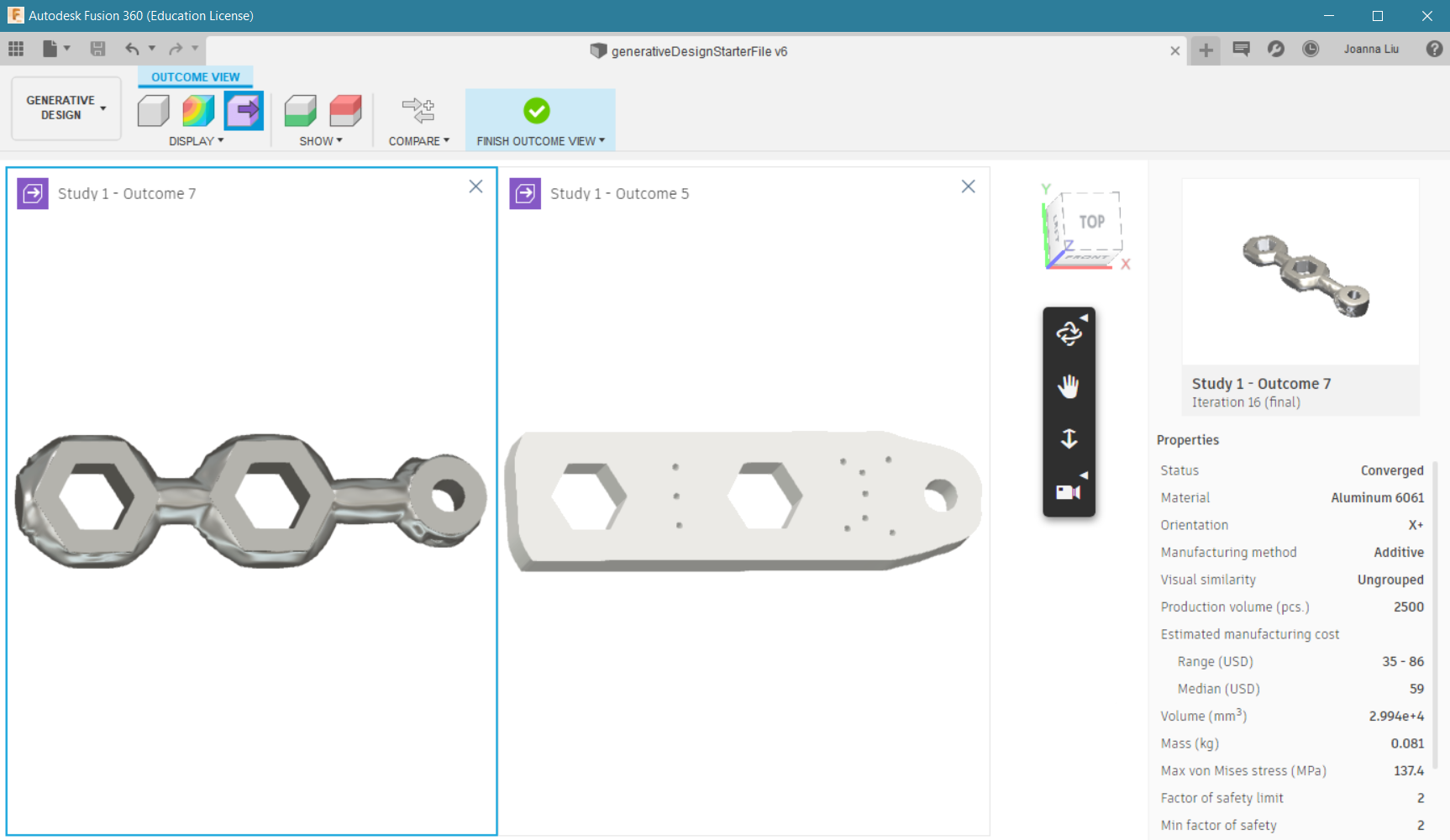
"Mill Tightening Wrench" - Practice with shape optimization, generative design, and material selection
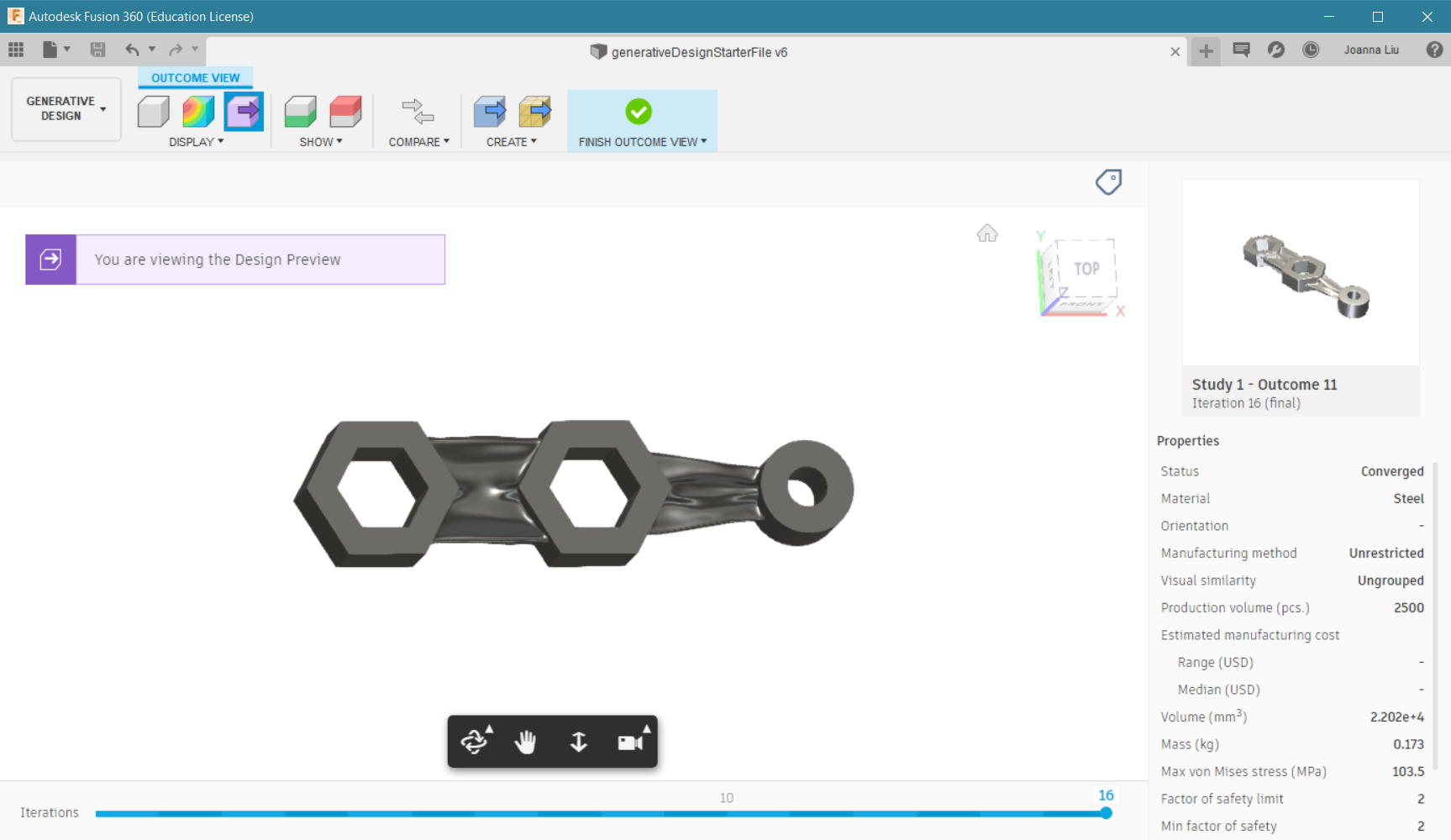
"Mill Tightening Wrench" - Practice with shape optimization, generative design, and material selection
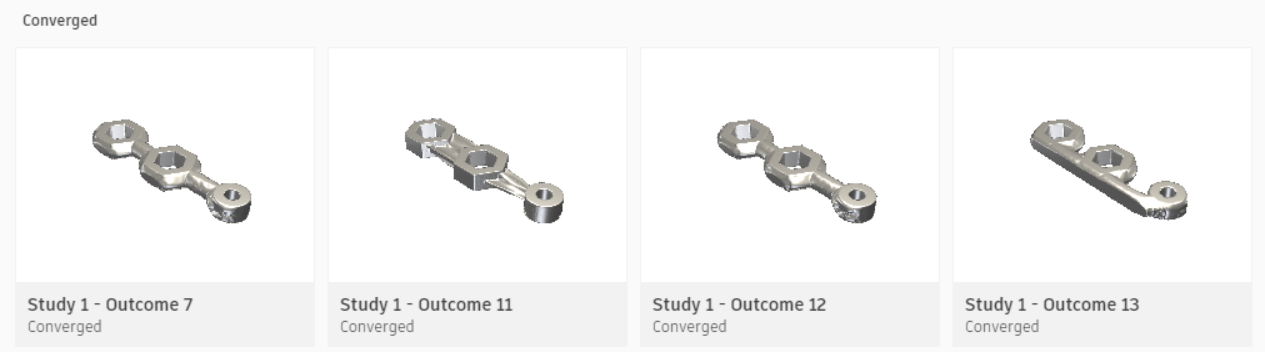
"Mill Tightening Wrench" - Practice with shape optimization, generative design, and material selection
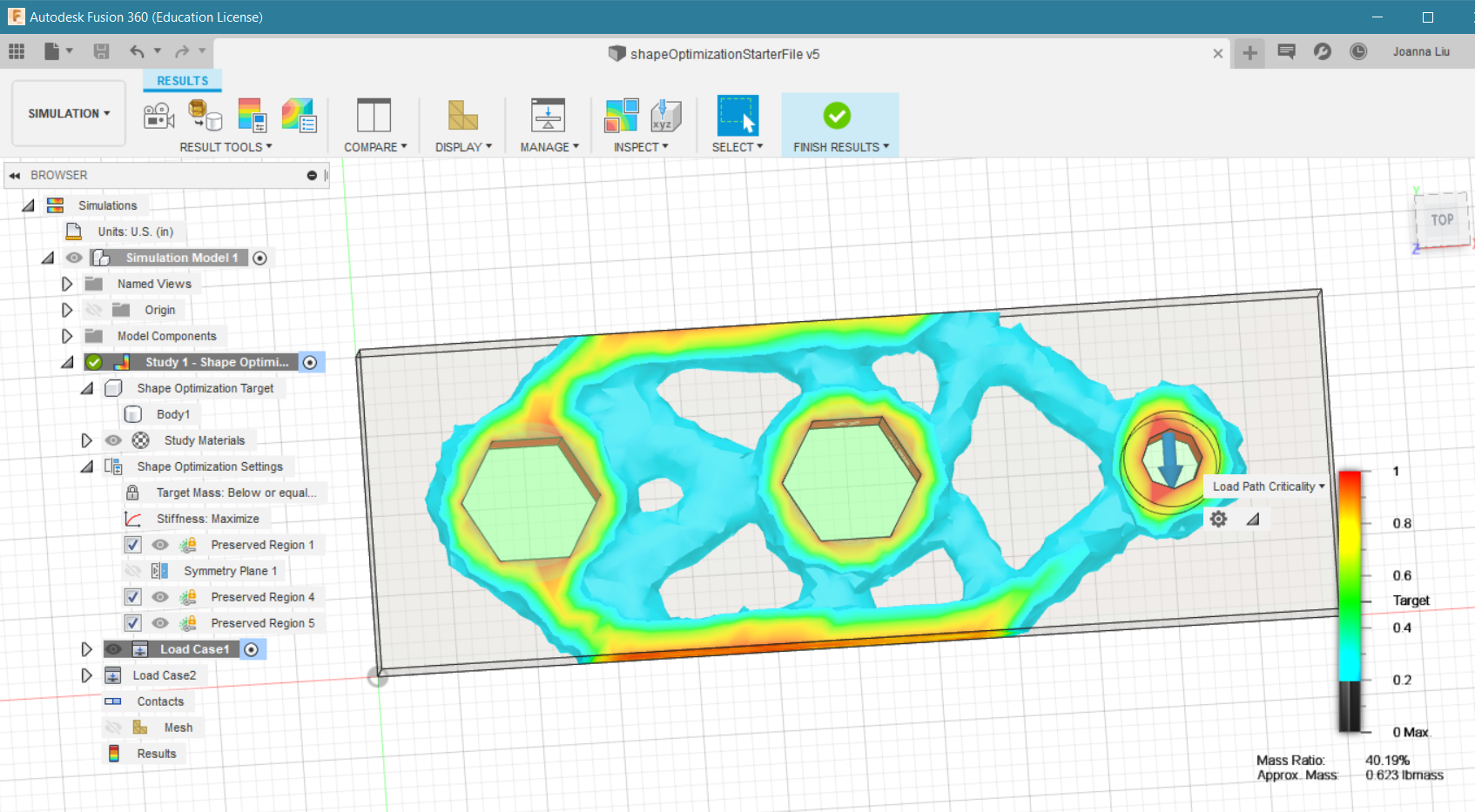
"Mill Tightening Wrench" - Practice with shape optimization, generative design, and material selection
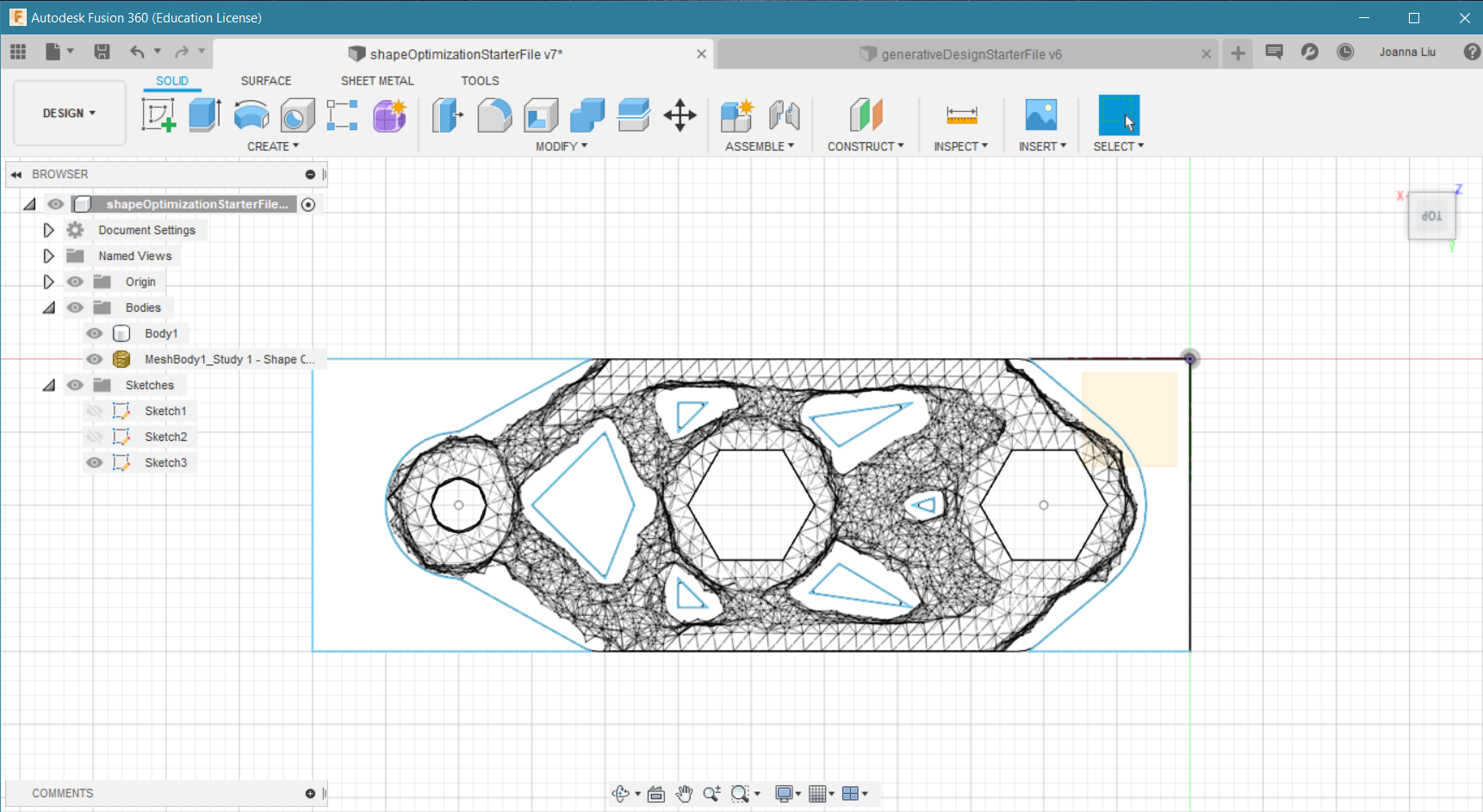
"Mill Tightening Wrench" - Practice with shape optimization, generative design, and material selection
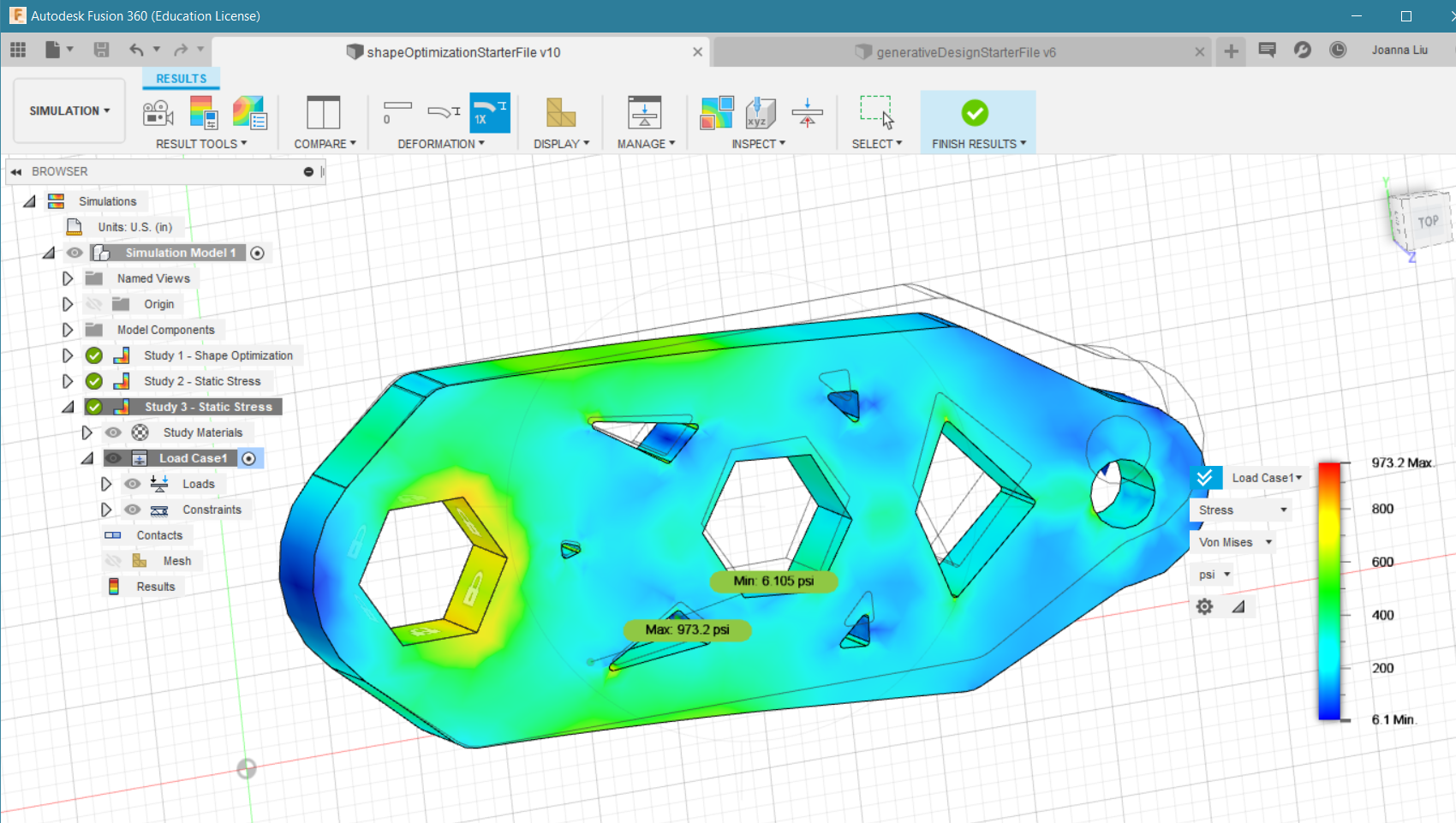
"Mill Tightening Wrench" - Practice with shape optimization, generative design, and material selection

"Pushup Bar" - Project focus on material selection and simulation for distributing large forces
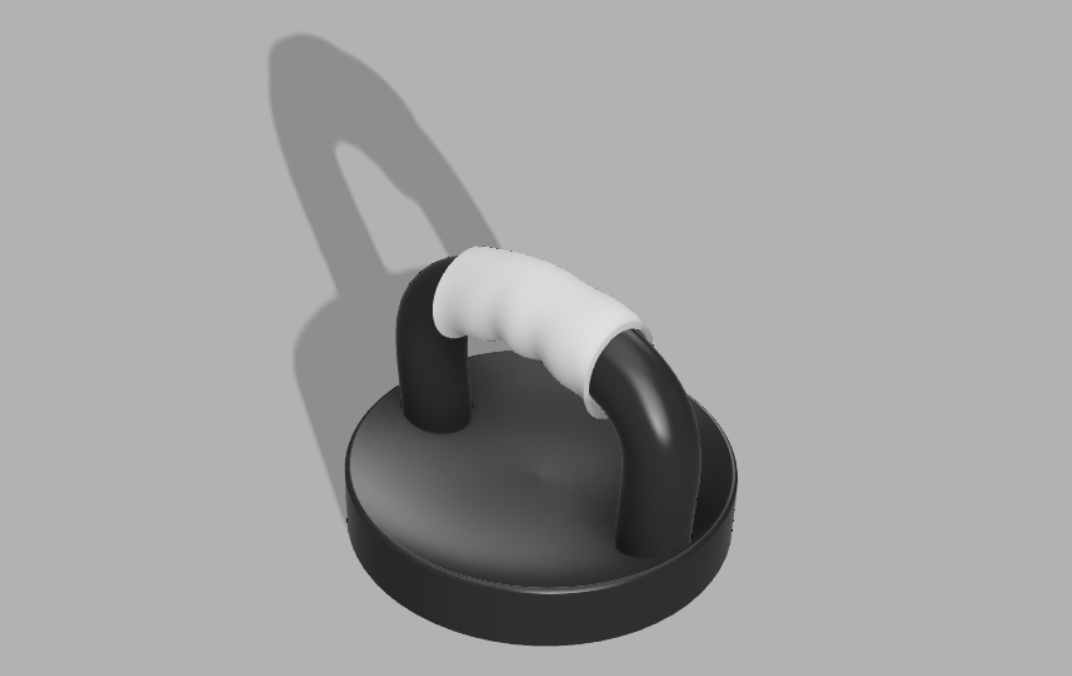
"Pushup Bar" - Project focus on material selection and simulation for distributing large forces